News
Partnership plans to scale cultivated meat production
21 Mar 2025Food technology innovator Ever After Foods (EAF) and multinational food leader Bühler are striving to overcome hurdles to access and accelerate the development of cultivated meat.
On 19 February 2025, foodtech innovator and cultivated meat producer Ever After Foods (EAF) and global food and feed industry leader Bühler announced their cultivated meat collaboration to progress and scale efficient and high-yield production for the global food manufacturing industry.

EAF and Bühler have teamed up to address the significant challenges in the global food chain, particularly the need to feed a growing population sustainably. The partnership plans to develop and introduce a commercial-scale cultivated meat production system.
“Scaling cultivated meat production and distribution is essential to provide a reliable and sustainable source of protein,” Eyal Rosenthal, CEO of EAF, told Ingredients Network. The duo believes this is crucial for meeting the protein demands of a growing global population while minimising resource use and environmental impact.
“Cultivated meat can be produced locally in urban areas, reducing reliance on long global supply chains and improving food security,” said Rosenthal.
Using innovative tech to develop cultivated meat
Technological advancement is at the centre of the duo’s joint commercial activities. The duo aims to bring commercially cultivated meat production to market at a ten-fold lower scale than existing market technologies.
Bühler seeks to produce and develop equipment to provide market-ready, sustainable, healthy, and affordable cellular products using biotechnology capabilities. EAF will utilise its patented production system, a proprietary edible packed-bed (EPB) technology platform, to develop cultivated meat production at scale.
The pair’s efforts strive to help the cultivated meat sector keep pace with the increasing global population’s growing protein demands.
“The global food chain faces significant challenges if we are to successfully and sustainably feed our growing population,” said Ian Roberts, CTO at Bühler. “How we produce and consume protein will continue to change, and our protein system must transition to deliver this,” Roberts added.
Replicating favourable meat properties, at scale
Combining food production and technology, EAF said that cultivated meat producers can lower production costs by over 90% while achieving production efficiency and gaining biological advantages, including enhanced nutritional value and superior flavour.
To date, EAF has deployed its technology to prompt the natural production of muscle and fat tissues for beef, chicken, duck, and fish cells. Utilising its patented system to maximise the sensorial experience of eating cultivated meat, EAF seeks to replicate conventional animal-derived meat in taste, texture, and overall enjoyment.
“Existing equipment and solutions from the biotechnology and pharmaceutical industries are not suitable for the food industry and cannot scale to meet the demands of cultivated meat production,” Rosenthal explained.
Gaining consumer approval
Overcoming regulatory and consumer acceptance obstacles will be key to the success of cultivated meat. “However, the main challenge for cultivated meat is the difficulty of scaling current technologies to achieve positive unit economics,” said Rosenthal.
The primary barrier to scaling cultivated meat production is the reliance on equipment and technologies adapted from the pharmaceutical industry, which are unsuitable for the cultivated meat industry. Mammalian cells are not well-suited to grow in large, stirred tanks, as they cannot survive the high mechanical stress imposed on them. To properly grow tissues, these cells require a solid environment mimicking natural growth conditions with very low mechanical stress.
“Due to the inefficient, high-stress environment of standard stirred-tank technologies, the cultured output is only around 2-4% of the working volume,” Rosenthal said.
For example, only around 4-8 kilograms of cultivated mass can be produced from a 200-litre reactor. “These limitations have hindered cultivated meat companies from scaling up to reactors with capacities of thousands of litres, which would be massive but necessary for profitable production,” Rosenthal added. Additionally, high equipment costs and long, unpredictable research and development timelines have made scaling up expensive and challenging to fund.
Instead of the 2-4% output typical of conventional methods, EAF’s technology and bioreactor system provide a low-stress environment to help achieve more than 40% cultivated mass per working volume. For instance, a 200L reactor can produce over 80kg of cultivated meat.
“This efficiency means we require up to 20 times lower scale to achieve the same output, significantly reducing development time, capital expenditures, and the amount and cost of growth medium needed,” Rosenthal said.
Related news

Future F&B flavours favour exploration and explosive taste profiles
25 Mar 2025
Exploration and experimentation will define the future of flavour, according to Mintel, as consumers seek out taste profiles and textures that offer an adventurous eating experience.
Read more
Global consumers enjoy food less and perceive it as less healthy
20 Mar 2025
Enjoyment of food and its perceived healthiness is dwindling among most global populations, according to findings from Gallup and Ando Foundation/Nissin Food Products.
Read more
Seafood set to ‘dethrone’ poultry as protein growth king
19 Mar 2025
Seafood is poised to surpass poultry as the leading contributor to global protein supply growth this year, according to Rabobank’s latest protein outlook.
Read more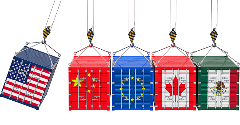
Tariff volatility leaves food manufacturers in limbo
11 Mar 2025
Rapid US trade policy shifts and tariff escalations are creating uncertainty for food manufacturers and ingredient suppliers.
Read more
F&B industry hit with fresh greenwashing claims
26 Feb 2025
The food and beverage (F&B) industry is under fresh scrutiny amid claims of greenwashing, with Arla the latest company in the firing line.
Read more
Protein diversification: A massive missed market?
20 Feb 2025
Germany and the UK could be missing out on the massive market for alternative meats and proteins, with one new coalition calling for an end to the “steak-tofu struggle”.
Read more
Have scientists discovered a new tool to measure UPFs?
19 Feb 2025
Researchers have developed a new scoring system and database, compiling over 50,000 food items, of which over 1,000 are classified as ultra-processed.
Read more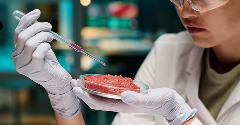
China ramps up cultivated meat research with new innovation base
18 Feb 2025
China has opened its first fermentation and cultivated meat research centre in Beijing.
Read more
Most consumers lack trust in AI, but supplement users are ready to embrace the technology
14 Feb 2025
A survey of UK and US consumers found that most supplement users are willing to let AI make decisions on their behalf, but they also demand greater transparency.
Read more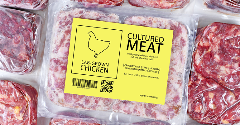
Indians enjoy first bites of cultivated chicken
13 Feb 2025
The first public tasting of cultivated meat in India has taken place as the country prepares for the first commercial cultivated meat products – potentially as early as the end of this year.
Read more